May 30, 2025
בלוג
Empowering Industry: The Rise of Connected Workers in Manufacturing
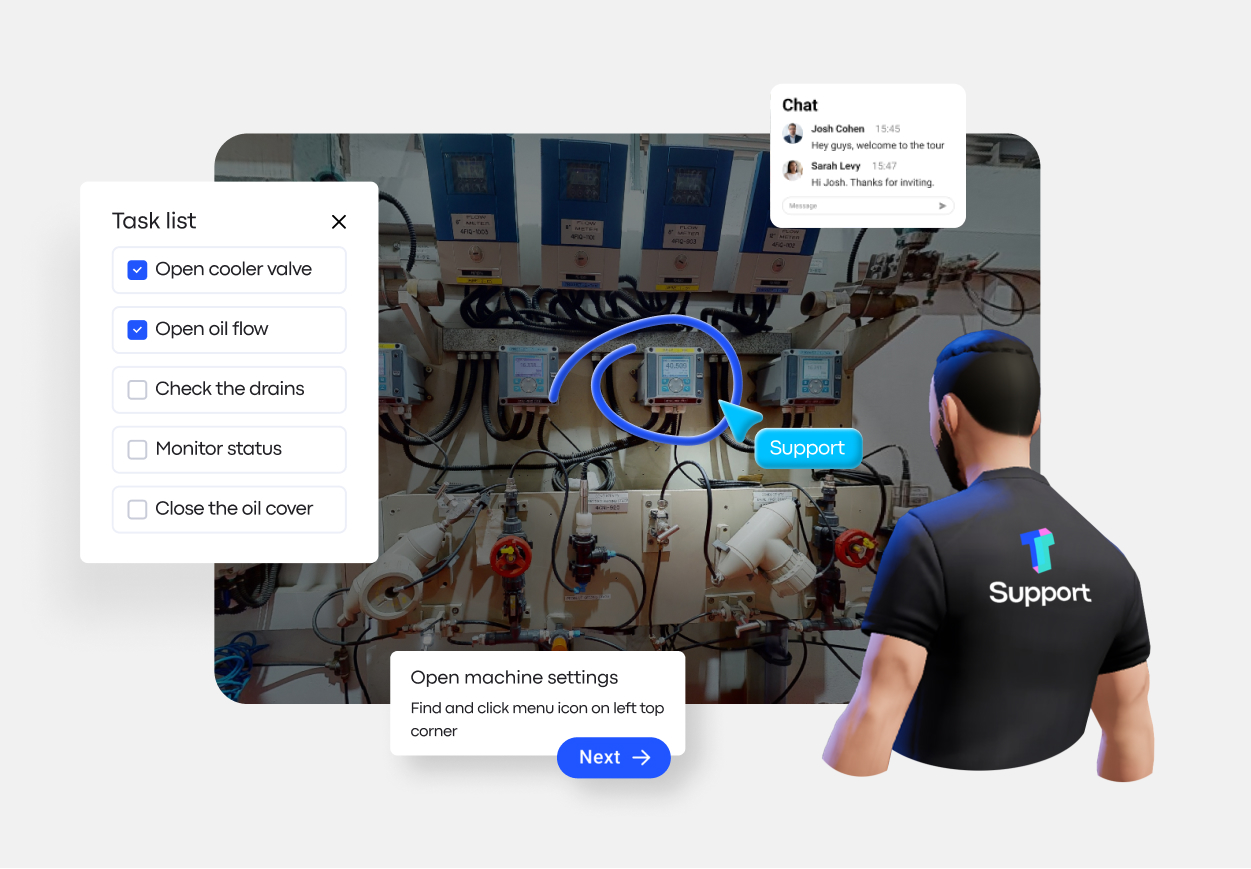
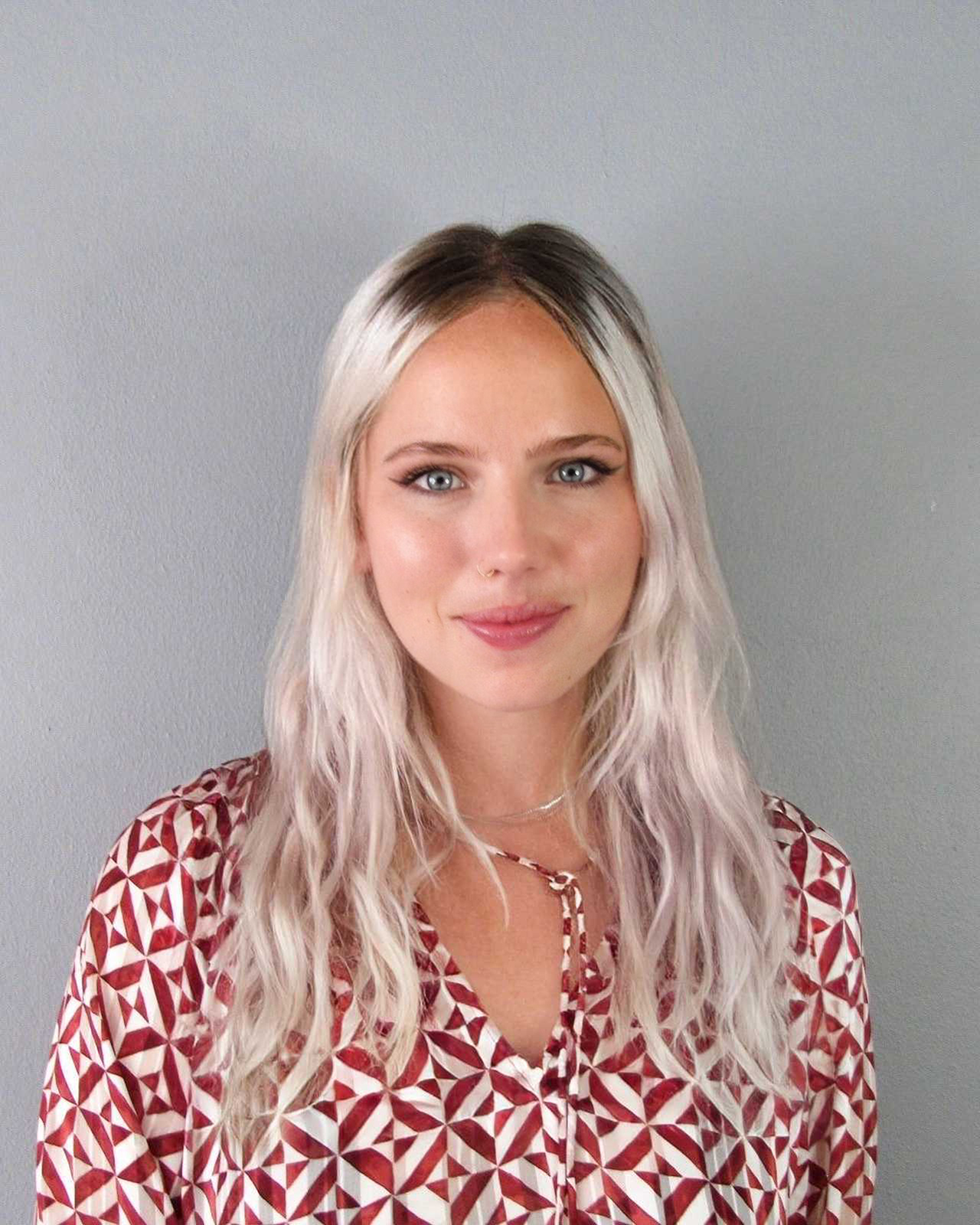
The manufacturing sector is undergoing a profound transformation, driven by the swift integration of automation and robotics, which have become central to enhancing productivity and transforming production processes.
But this advancement does not diminish the role of human workers. Far from making humans obsolete, the rise of smart machines has highlighted the need for human-machine collaboration. This synergy is becoming the cornerstone of modern manufacturing networks, reshaping how we view the interplay between man and machine in creating the future of industry.
This pivotal shift brings us directly to the concept of the "connected worker," a theme we will explore in depth throughout this blog.
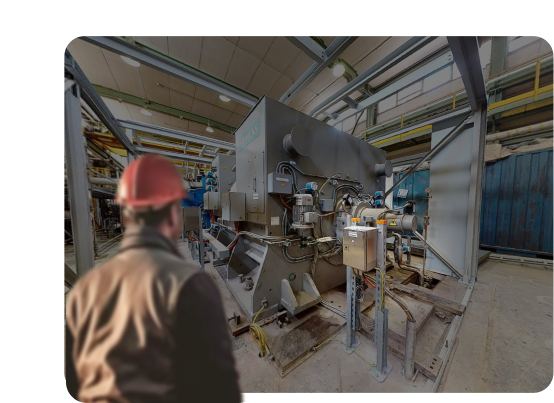
What Is the Role of Connected Workers in Modern Manufacturing?
Connected workers are workers that are integrated with their industry’s products, processes, and people.
This integration needs to take a comprehensive approach, connecting workers to digital resources and technologies that bolster their skills, safety, and efficiency. They need to be able to collaborate with their team, supervisors, experts, and even customers using technologies that enable remote interaction and collaboration.
Connected workers also benefit from digital tools that offer real-time assistance and training based on standard protocols. These tools are pivotal not just for training newcomers but also for preserving and sharing organizational knowledge and practices, ensuring easy access and implementation by all employees.
Why Are Connected Workers Essential for Industry Efficiency?
The expectation for immediate information access constantly rises, placing significant pressure on frontline workers like manufacturers, assembly engineers, and warehouse personnel.
These workers find themselves at a crossroads, tasked with executing today's duties at an accelerated pace, yet often equipped with tools and methodologies that are outdated. Essentially, they're caught in a push to meet the demands of the future with the resources of the past.
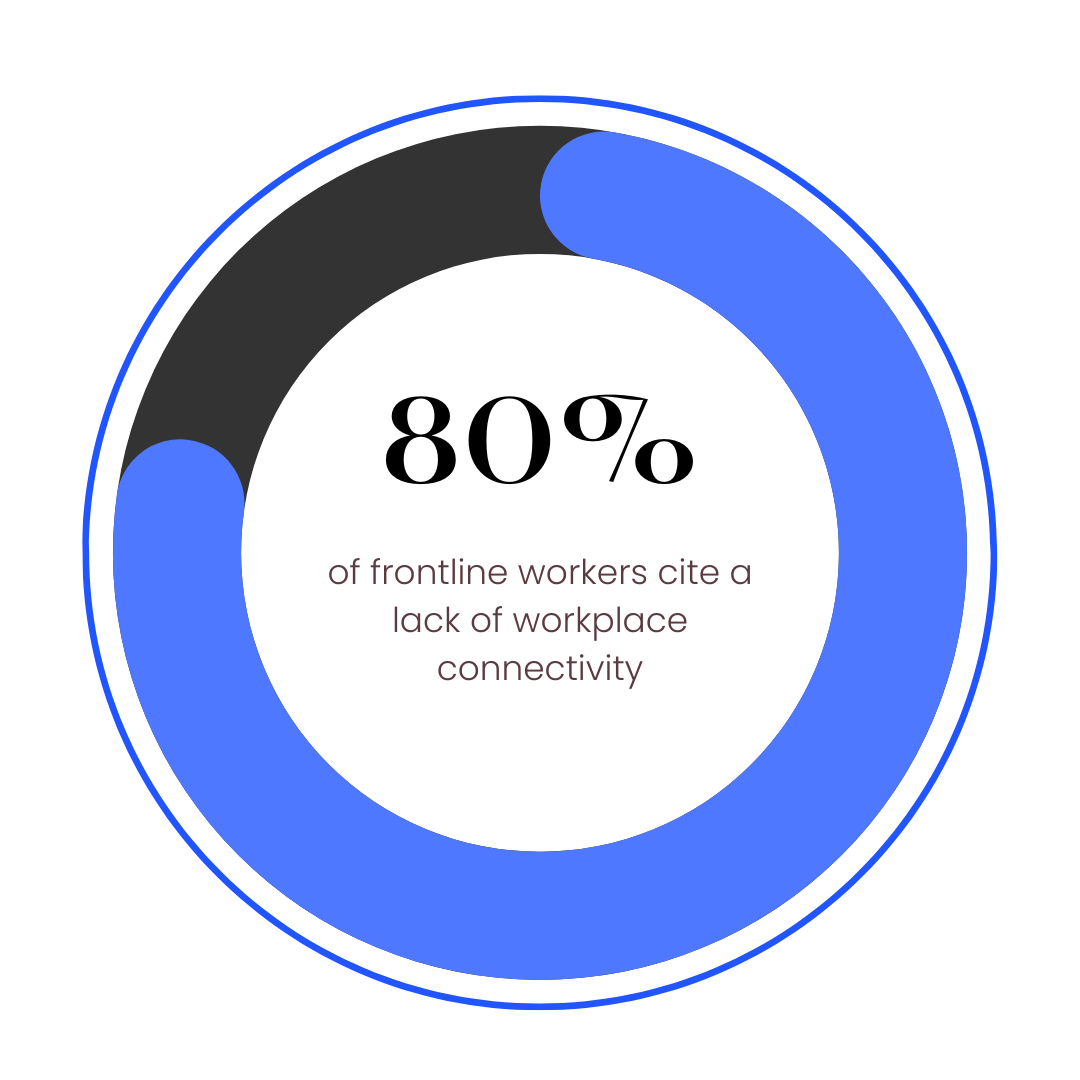
This sentiment holds especially true for frontline workers who, despite numbering an estimated 2.8 billion globally, are notably overlooked in the digital transformation era, leading to a widening skills gap. Only 23% of frontline workers report having the technology needed for productivity, and 80% cite a lack of workplace connectivity.
These challenges can be overcome with a comprehensive connected workers solution that is both easy to implement and easy to scale. Connected workers have the advantage of timely, contextual access to necessary resources right where and when they need them. Information that once required pausing a task to consult a manual or an expert is now instantly available, reducing wait times for supervisor responses from days to moments.
When equipped with the right tools, frontline workers can see their productivity increase by an average of 22%. This boost in efficiency means tasks can be completed more quickly and accurately, leading to cost savings by reducing overtime and the need for additional hires.
What Technologies Drive Productivity for Connected Workers?
Identifying the right tools to boost frontline worker productivity is crucial. The following technologies emerge as non-negotiable keystones in any connected worker solution that truly carries its weight in gold.
- The Internet Of Things (IOT)
A connected worker needs to be connected to technology. This is where IoT comes into the picture.
IoT consists of networked devices, sensors, and software to collect data and information technology (IT) and Operational Technology (OT) systems, contextualise the data and turn it into meaningful insights through the internet.
The adoption of IoT has been on the rise in the last decade, with 15.41 billion devices in 2015, nearly tripling to 42.6 billion by 2022 and expected to reach 75.44 billion by 2025.
The reason behind this widespread adoption is a no brainer. IoT is pivotal in creating the infrastructure for data collection and communication among devices, workers, and systems. It facilitates the monitoring of equipment performance, anticipates maintenance needs, and ensures the safety of the workforce.
When frontline workers have comprehensive access to these IoT sensors, they are able to gain a full understanding of the state of the different technologies that they are working with.
But this data is traditionally siloed, making it difficult for workers to understand all of the processes going on in an organization. It’s not enough to just gather data, workers need to be able to make sense of it in a way that breaks down old barriers with a more intuitive visual space that helps frontline workers grasp insights faster and get up to speed with standard operating procedures more quickly.
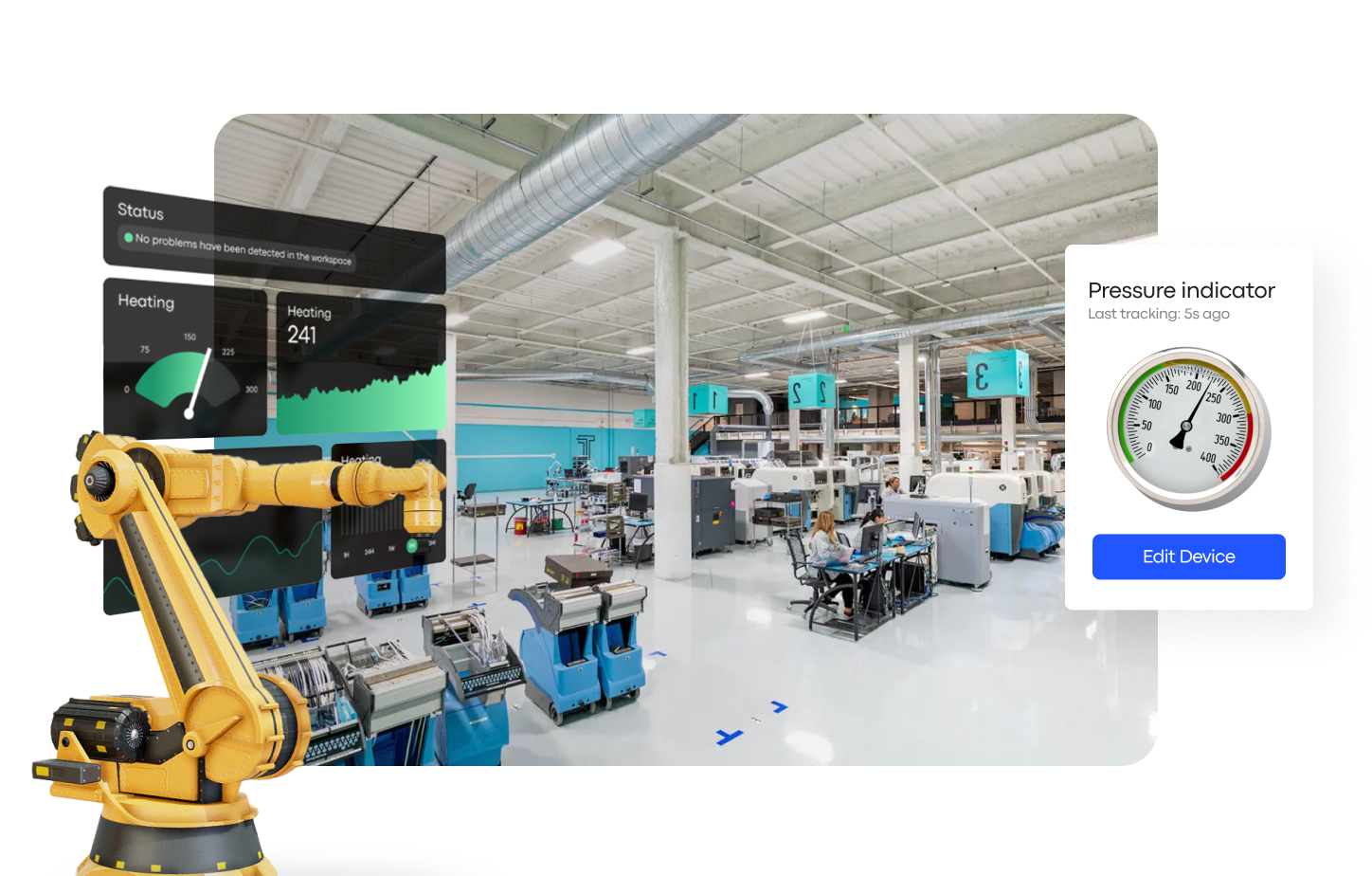
- Integrated Digital Twins
A digital twin is a virtual replica of a real space. When it comes to the manufacturing industry, a digital twin is useful for mapping out the different machinery. When integrated with IoT sensors, they serve as a unified 3D digital dashboard that gives a comprehensive view of all processes on the plant.
Digital twins can then also complement IoT as a monitoring or decision making support tool by offering a dynamic digital replica of physical entities, allowing businesses to simulate scenarios, monitor systems in real-time, and test changes virtually, thus enhancing decision-making and risk management. The establishment of a connected physical and virtual twin (Digital Twin) helps address the issue of seamless integration between IoT and data analytics.
Frontline workers and all of the team can then have immediate access to these insights.
- Augmented and Virtual Reality (AR & VR)
Once a digital twin integrated with IoT sensors is established, AR and VR solutions for maintenance and training can be implemented to enhance standard operating procedures onboarding.
AR transforms traditional worker training methods by providing immersive, interactive experiences that improve learning outcomes. It overlays digital information onto the physical world, offering step-by-step instructions and insights into complex machinery and processes. Virtual training platforms using digital twins build upon this by creating fully immersive environments for skill practice and scenario simulation, preparing workers for various situations without real-world risks.
But the buck does not simply stop at training. Once these sops are digitized in this way they can be accessed for a range of maintenance processes as well. More than that, when IoT is connected this data can also be accessed and connected through AR, making it as quick and easy for the frontline worker to check on the status of the equipment as it is for the remote supervisor. It also combats the forgetting curve that workers often face with practical training, ultimately resulting in reduced downtime.
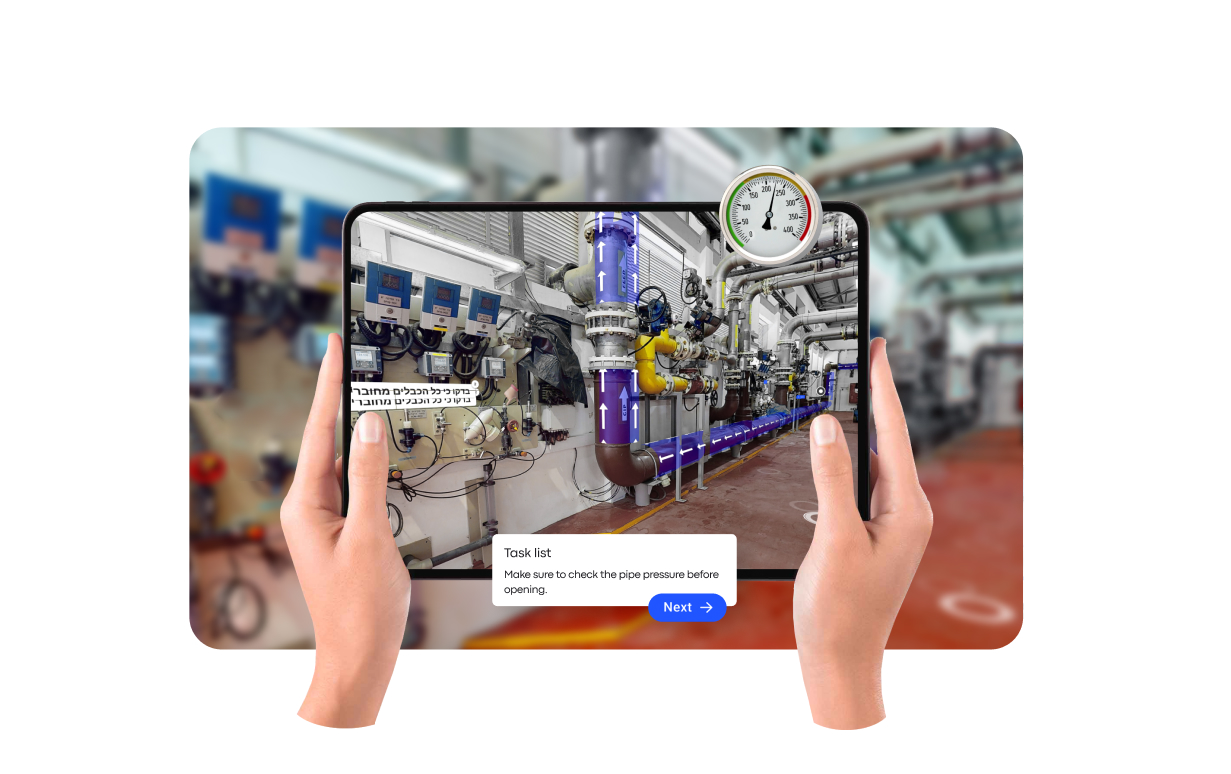
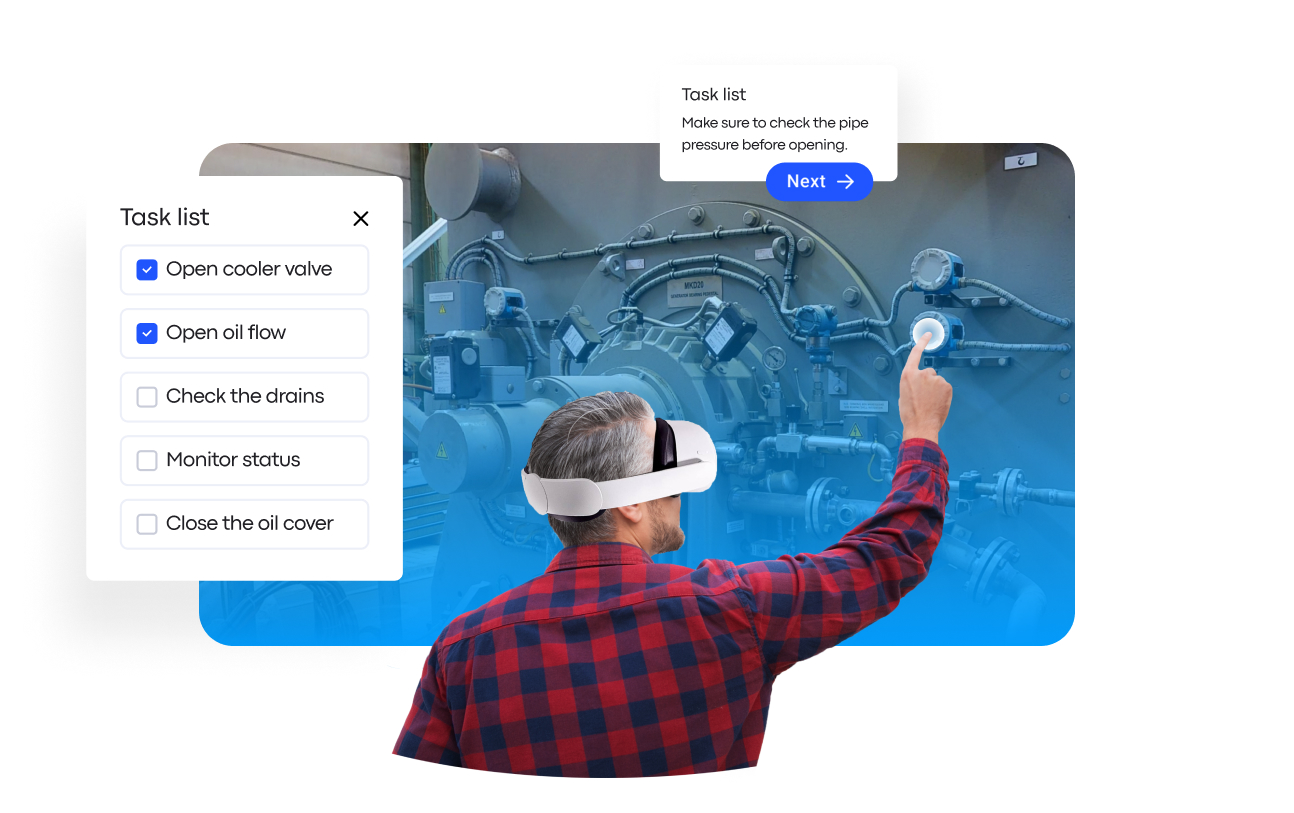
What Are the Advantages of Implementing a Connected Worker Solution?
Now that we've thoroughly explored the essential components of a connected workers solution, let's delve into the compelling reasons why numerous companies are embracing this innovative approach.
- Reduction in unplanned downtime
Over two-thirds of industrial enterprises reported experiencing unplanned downtime on a monthly basis, with an average hourly cost of $125,000. Additionally, apart from the evident direct financial implications, downtime brings about various indirect costs such as damage to reputation, potential health and safety hazards, decreased team morale, and increased insurance premiums.
Unplanned downtime can be a result of an operator error, tool and equipment failure, lack of communication, and poor planning.
These causes can be mitigated by connecting your workers effectively to the machines, technologies, processes, and people around them.
Enforcing standard operating procedures is a crucial way of minimising unplanned downtime as this ensures that everyone is working in the same way.
- Improved Safety and Compliance
Connected Worker Solutions can improve safety by providing workers with instant access to safety procedures and real-time hazard alerts. These solutions help ensure that safety protocols are followed more consistently and can enable faster response in case of an emergency, reducing the risk of accidents and ensuring regulatory compliance.
- Better Training and Support
With AR and VR, training and onboarding processes can be enhanced to provide more interactive and engaging learning experiences. These technologies can simulate real-life scenarios for practice without the risks associated with on-the-job training. Additionally, AR can provide on-the-job support by overlaying digital information onto the physical world, helping workers perform tasks with greater precision and confidence.
- Increased Worker Satisfaction
By reducing manual and repetitive tasks through automation and providing tools that help workers do their jobs better, Connected Worker Solutions can lead to higher job satisfaction. Workers feel more empowered and engaged when they have access to technologies that help them succeed. This can lead to lower turnover rates and a more motivated workforce.
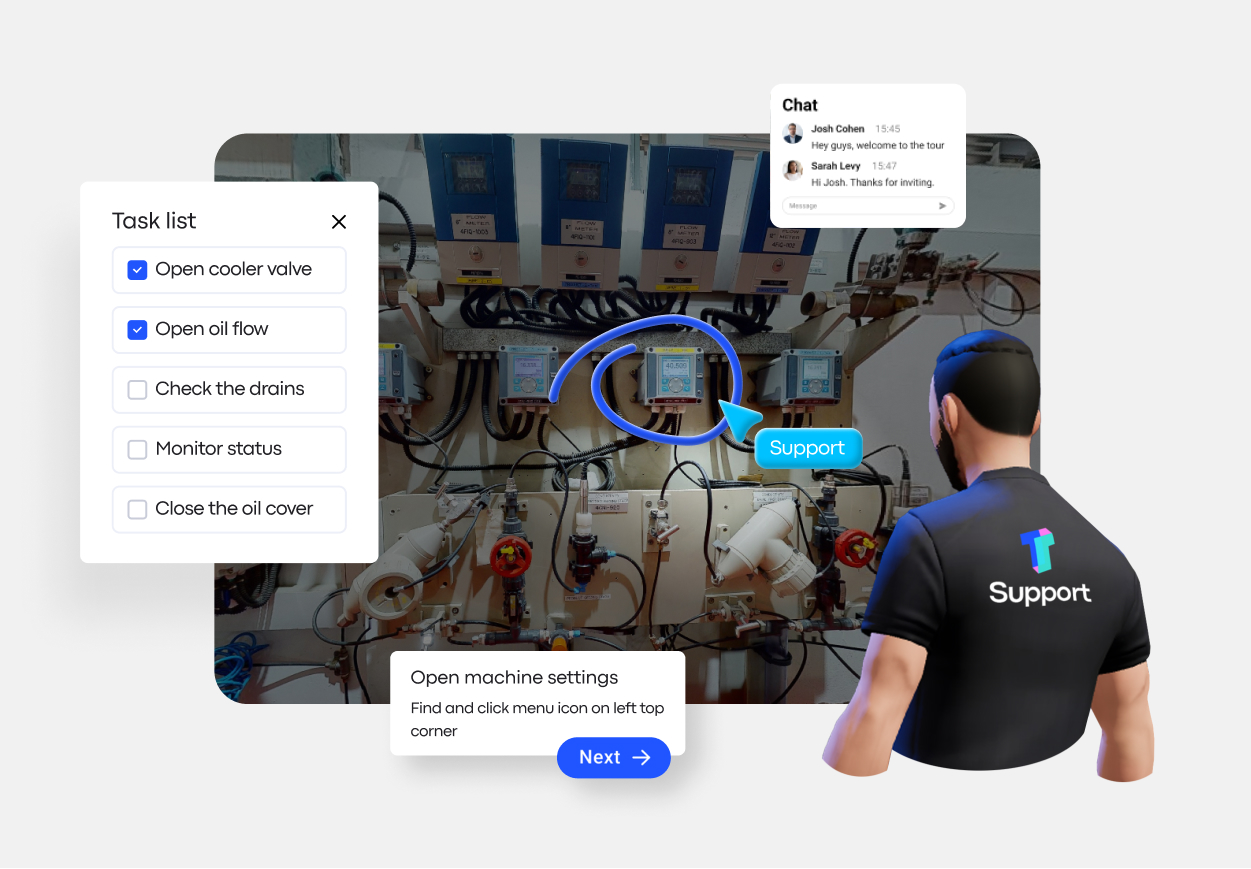
Who Are the Leading Providers of Connected Worker Solutions?
- Treedis
Treedis provides a connected workers solution that enhances industrial operations by integrating digital twin technology, augmented reality (AR), virtual reality (VR), and the Internet of Things (IoT). This solution allows for the creation of digital replicas of physical environments, which can be interactively layered to aid in operational management and training. AR and VR technologies are employed to offer immersive training and maintenance experiences, making complex tasks more accessible and engaging. IoT integration supports real-time monitoring and control, boosting decision-making and operational efficiency.
Furthermore, Treedis enables the customization of digital twins through no-code editing tools, catering to specific business needs. This comprehensive approach not only increases efficiency and reduces downtime but also enhances safety protocols and supports collaborative efforts among remote and field employees.
- Tulip
Tulip's connected worker solution integrates workers into their digital and physical environments using advanced technologies such as IoT devices, real-time data analytics, and apps. This platform enhances worker efficiency, safety, and decision-making in manufacturing settings by providing digital work instructions, quality management tools, and machine monitoring capabilities.
- MaintainX
MaintainX offers a connected workers solution focused on industrial and frontline teams. It provides a mobile-first platform designed to streamline maintenance operations and enhance asset management. MaintainX features include the management of work orders, simplified work order execution with dynamic SOPs, and real-time tracking of work order performance.
- Notify
Notify's connected workers solution enhances workplace safety and compliance across various industries by facilitating real-time incident reporting and management. Using a mobile app, workers can quickly report hazards, near misses, and incidents, which enables proactive safety management. The platform includes tools for risk assessments, method statements, action tracking, audits, and inspections, all centralized within a comprehensive document management system. This setup not only improves incident response times but also promotes a culture of safety and compliance within organizations, ultimately helping to reduce workplace accidents and ensure regulatory compliance.
- GoARC
GoARC provides a connected workers solution that enhances safety and efficiency in industrial settings through an integration of IoT, AI, and real-time data analytics. Their system utilizes wearable devices to monitor worker vitals and environmental sensors to detect hazardous conditions, all linked to a central analytics platform. This platform processes the data to predict risks and initiate preventive measures, improving safety and operational productivity.
How Can Smart Manufacturing Solutions Optimize Costs and Efficiency?
The costs associated with acquiring and deploying these advanced technologies can be substantial when multiple vendors are consulted. That’s why it’s important to find a connected workers solution that provides a unified, and scalable, architecture.
When out of the box solution offerings are consulted, the implementation costs for smart manufacturing systems decrease. The average cost of IoT sensors has also reduced by 37% between 2004 and 2020, highlighting the increasingly accessible nature of advanced technology for businesses of all sizes.
This reduction in sensor costs aligns with the broader trend of technological innovation driving down the barriers to entry for adopting smart manufacturing practices, ultimately fostering greater efficiency, agility, and competitiveness in the industry.
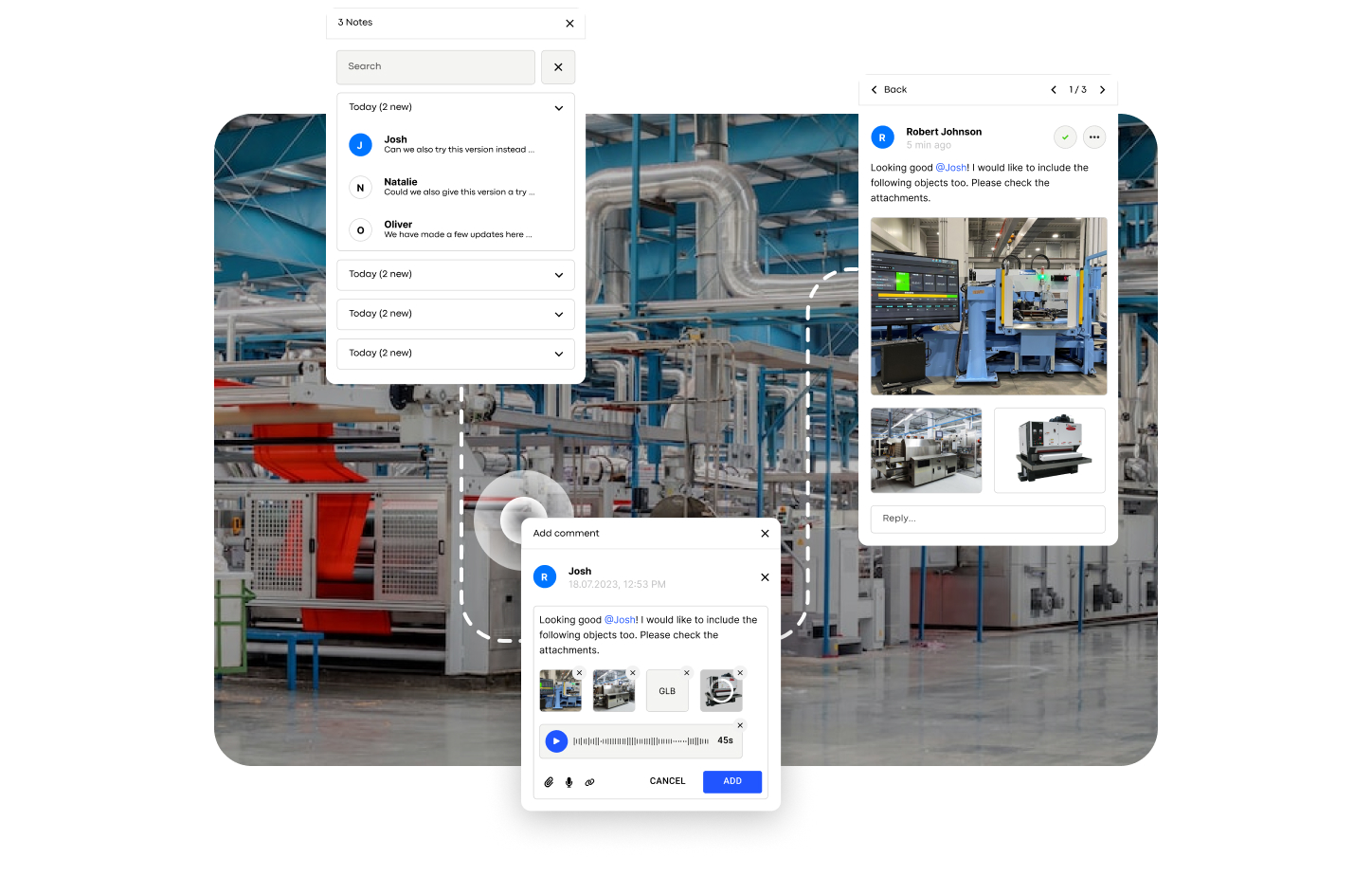
What Does the Future Hold for Manufacturing with Connected Workers?
As we look ahead in manufacturing, the role of connected workers is becoming increasingly vital. Embracing this concept doesn't just mean adding new technologies; it's about making daily tasks more intuitive and efficient for the people at the heart of the industry.
This shift towards connected working environments is about enhancing collaboration and providing real-time support that helps workers do their jobs better and with greater satisfaction.
By integrating these solutions, businesses can ensure their teams are well-prepared to meet future challenges, making their operations smoother and more adaptive to changes. This isn't just about staying competitive; it's about creating a workplace where technology and human talent work hand in hand for smarter manufacturing.
מאמרים נוספים
מאמרים נוספים
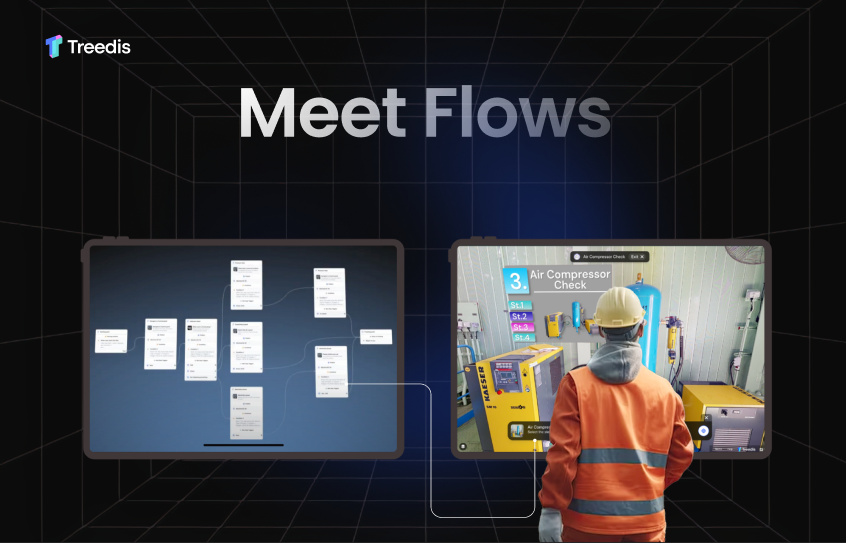
May 30, 2025
Future-Proofing Operations with Flows
Want your team to train better? We have your solution. This blog breaks down our standout feature, Flows, showing it's potential for your organisation.
.png)
Jan 14, 2025
How Immersive Technologies Are Revolutionizing Workforce Training and Closing the Skills Gap
Immersive technologies like AR, VR, and digital twins are revolutionizing workforce training by addressing the growing skills gap with engaging, hands-on learning experiences. These solutions enhance retention, boost productivity, and reduce costs, making them essential for dynamic, scalable training in a rapidly evolving job market.
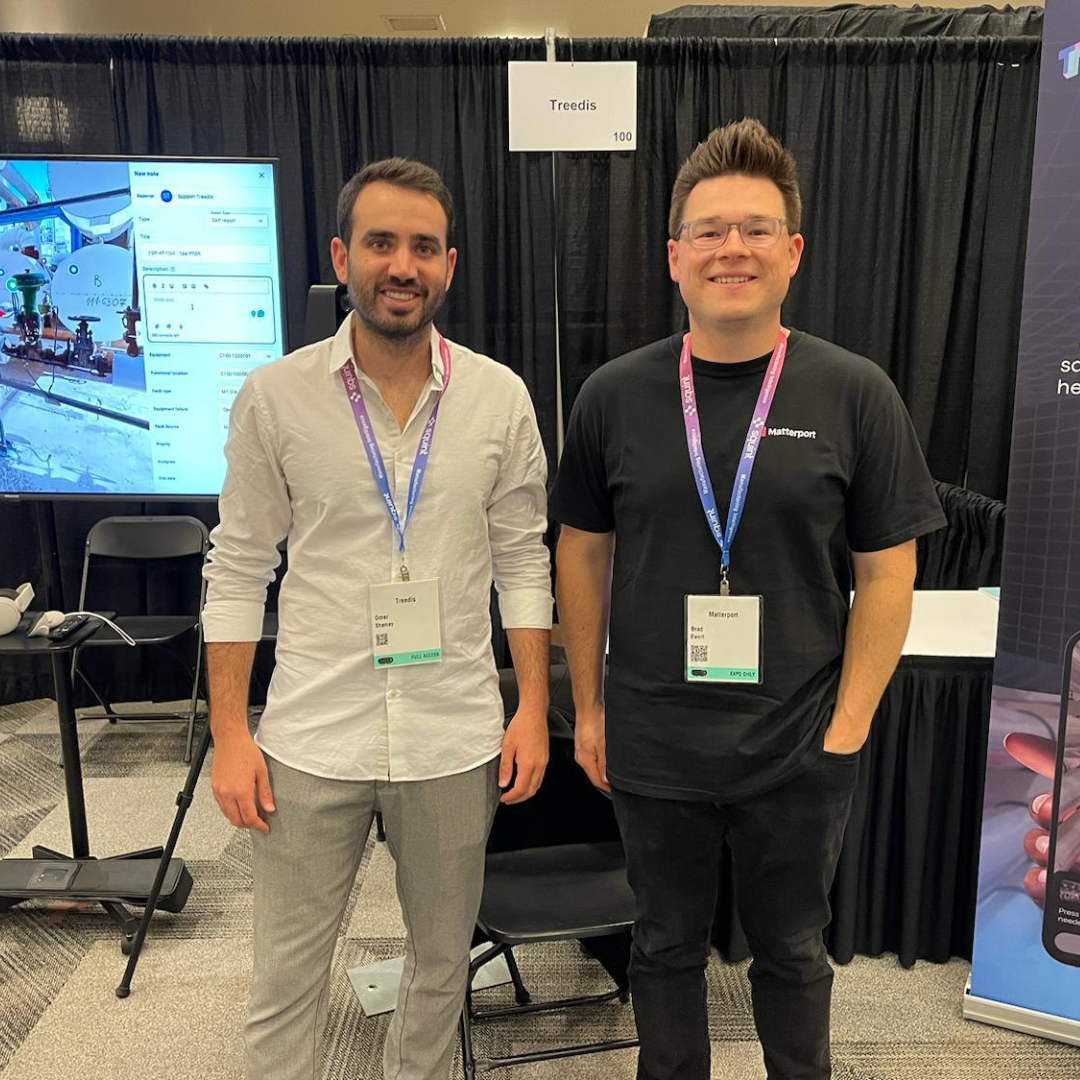
Nov 27, 2024
What's Next For Training? Takeaways From The Augmented Enterprise Summit
In October, we joined the Augmented Enterprise Summit (AES) with Matterport, connecting with industry leaders and Fortune 500 companies while sharing key XR insights.
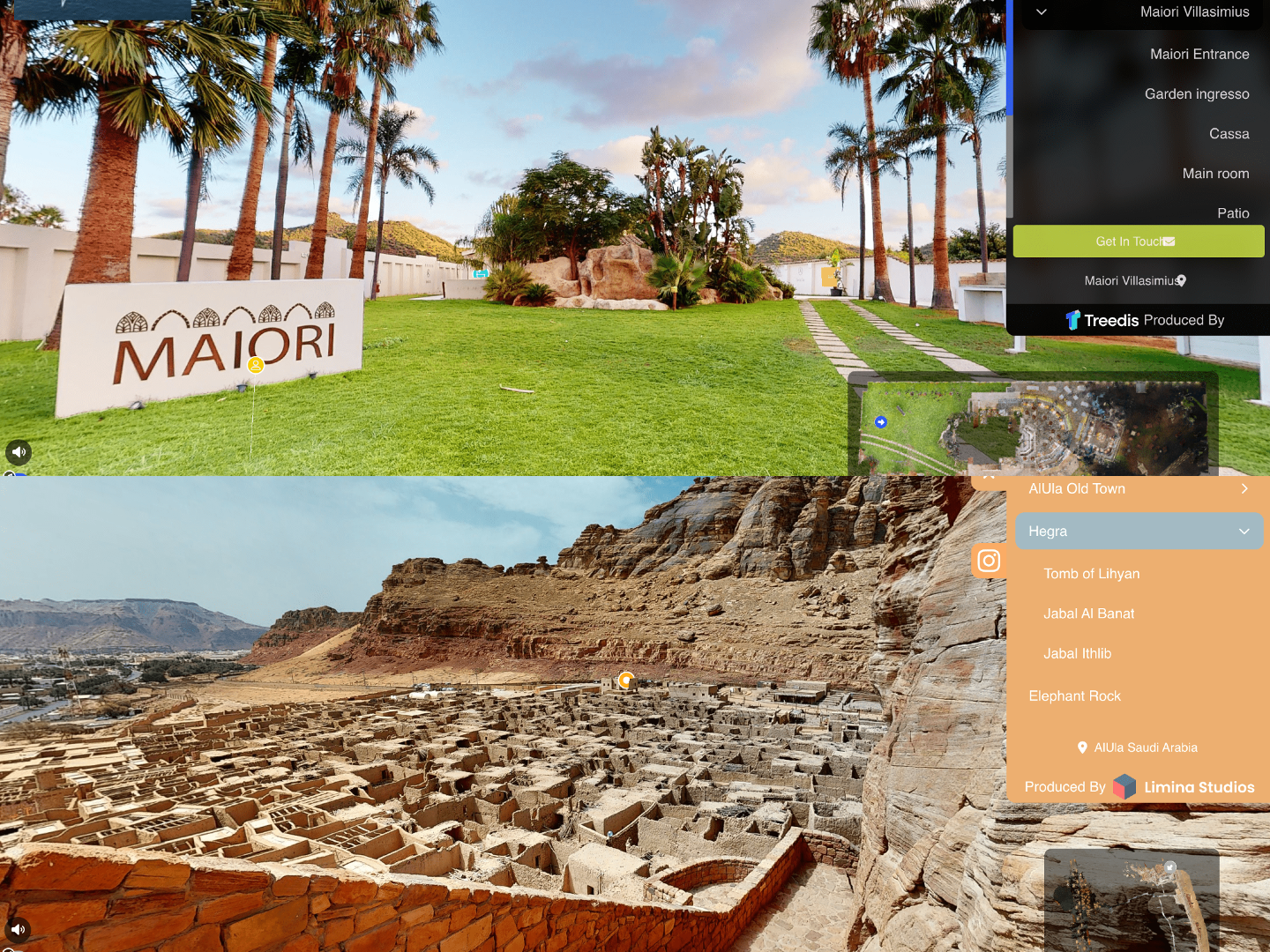
Jun 28, 2024
Digital Twin Awards: Success Stories
The Digital Twin Awards honor virtual tour innovation. This year, Treedis users Farhad Berahman from Limina Studios and Francesco Loddo from SardiniaVirtualTours3D won in historical and hospitality categories. Farhad's tour of AlUla captivated 2 million viewers, while Francesco's tour of Maiori Villasimius boosted bookings by 25%. Their achievements showcase the transformative power of Treedis technology.
%20(1).jpg)
Jun 5, 2024
Key Insights from Hannover Messe: The Future of Manufacturing in Industry 4.0
At the 2024 Hannover Messe, Treedis showcased its Connected Workers solution with AWS, Vodafone Business, and Matterport, integrating digital twins and live sensor data to enhance manufacturing efficiency. This collaboration highlighted the importance of strategic partnerships in advancing Industry 4.0. Treedis remains committed to providing scalable, innovative solutions for the evolving manufacturing landscape.